AI in Manufacturing: Production Line
AI in Manufacturing: Production Line Optimization
- Identify bottlenecks: Analyze the production line to pinpoint slow or inefficient steps.
- Implement automation: Introduce automated machinery for repetitive tasks to increase speed and consistency.
- Streamline workflows: Organize the production process to minimize delays between steps.
- Train employees: Offer training to improve worker efficiency and skill levels.
- Monitor and adjust: Regularly review performance data to identify improvement areas and adjust processes accordingly.
The Importance of Production Line Optimization
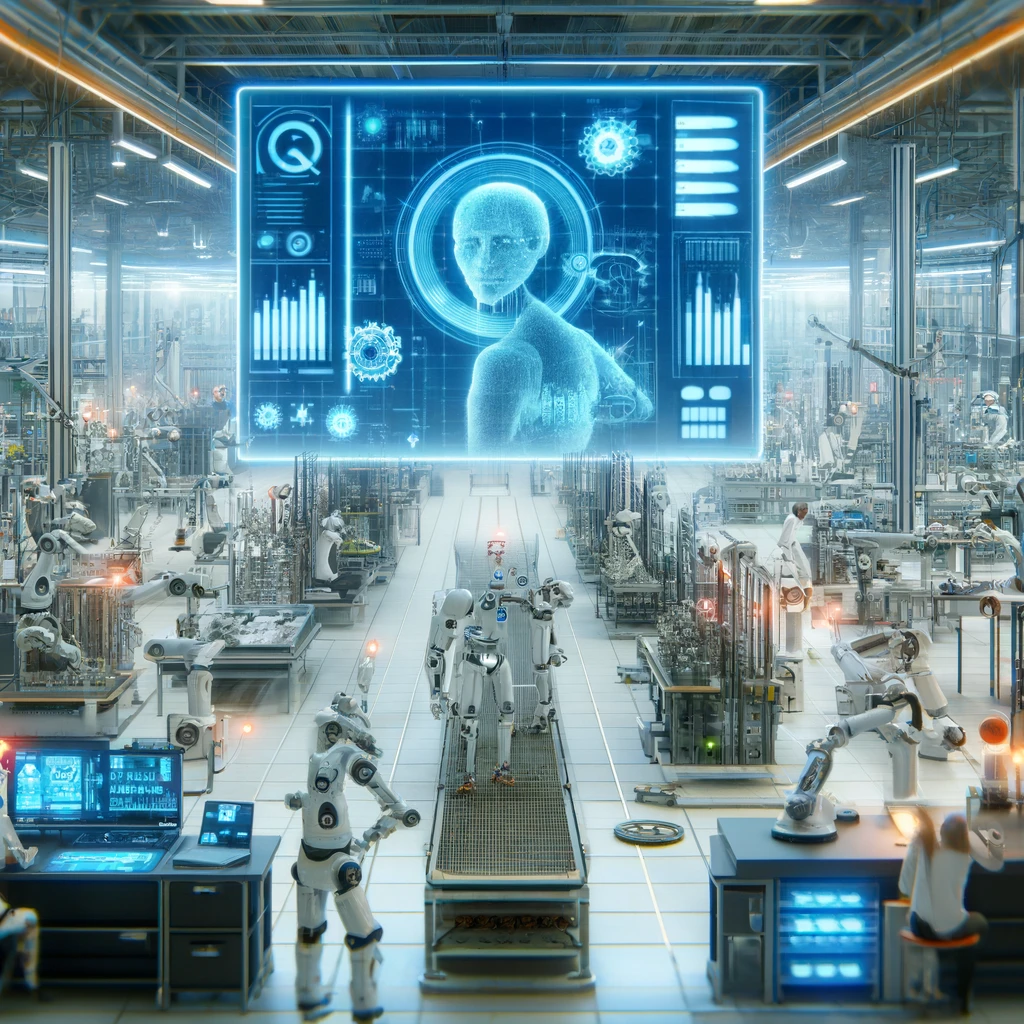
Production line optimization is the process of refining manufacturing operations to achieve maximum efficiency, quality, and throughput.
In the competitive landscape of the manufacturing sector, the ability to streamline production processes stands as a critical factor for success.
- Significance in Manufacturing: Optimization efforts focus on minimizing bottlenecks, reducing downtime, and ensuring that resources are utilized effectively. By doing so, manufacturers can significantly enhance their production capacity and operational efficiency.
- Direct Benefits:
- Cost Savings: Streamlining production processes leads to a direct reduction in operational costs. Efficient use of materials, labor, and energy lowers overall production expenses.
- Increased Output: Optimization enables manufacturers to increase production volumes without additional resources or extended work hours.
- Sustainability: Reducing waste and improving resource efficiency contribute to more sustainable manufacturing practices, aligning with environmental goals and regulations.
AI’s Role in Improving the Manufacturing Processes
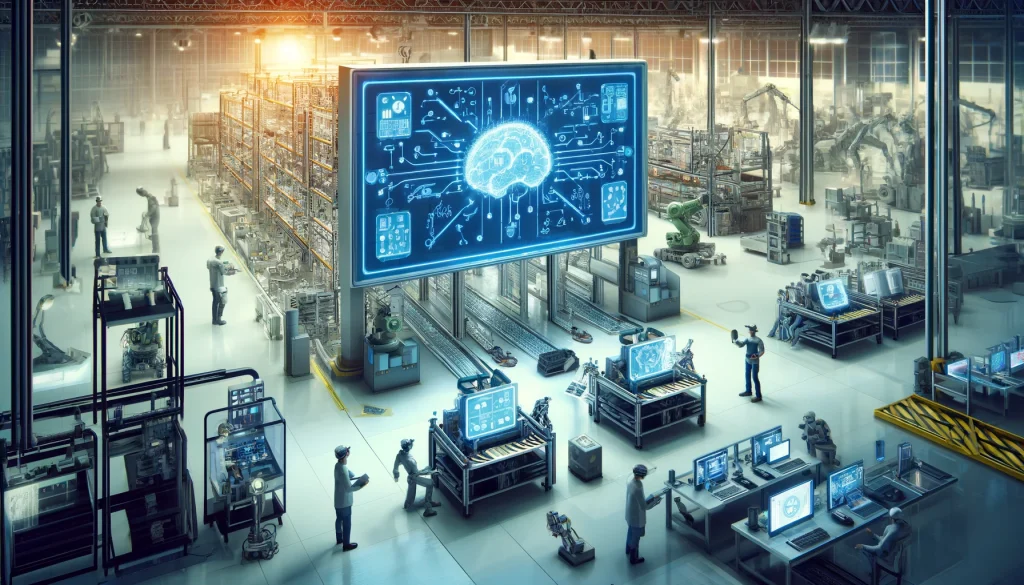
Artificial Intelligence (AI) is at the forefront of the technological revolution in manufacturing, offering sophisticated solutions to complex optimization challenges.
- Revolutionizing Manufacturing Operations: AI technologies are instrumental in transforming traditional production lines into smart, adaptive systems capable of self-optimization. By analyzing data in real-time, AI identifies inefficiencies and suggests actionable improvements.
- AI Tools and Methods:
- Data Analytics: AI-powered data analytics tools process vast amounts of production data to uncover insights into operational inefficiencies, quality control issues, and maintenance needs. These insights inform strategic decisions to enhance productivity and reduce costs.
- AI-Driven Simulation Models: These models allow manufacturers to simulate different production scenarios and predict their outcomes without disrupting operations. By testing various configurations, schedules, and processes, manufacturers can identify the optimal setup for their production lines before implementing any changes physically.
Through data analytics and simulation models, AI empowers manufacturers to anticipate problems, adapt to changes in demand, and continuously refine their production processes.
This proactive approach to optimization boosts operational efficiency and enhances manufacturing businesses’ agility and competitiveness in the global market.
Data Analytics in Manufacturing
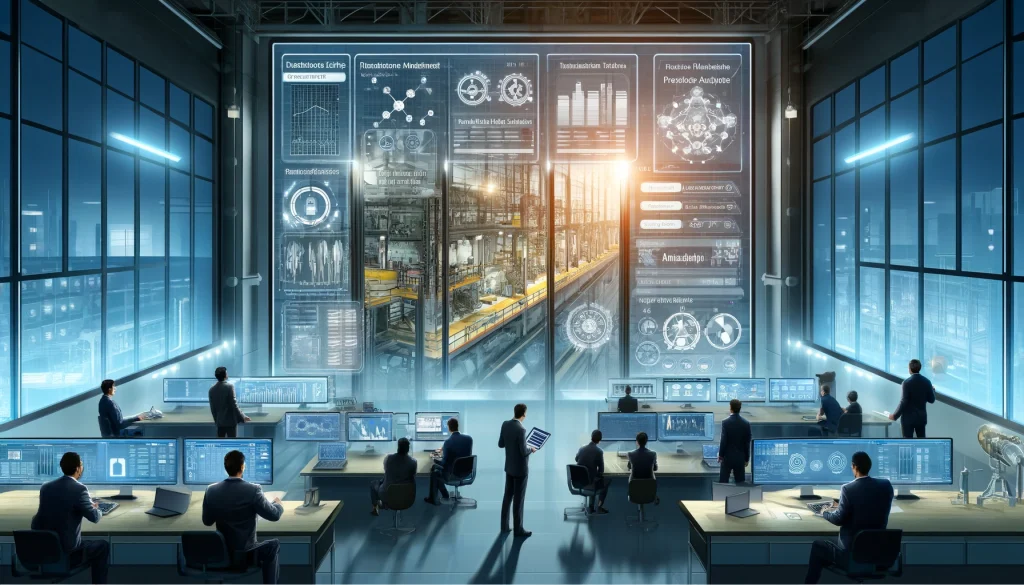
Data analytics has become a linchpin in modern manufacturing, offering deep insights that drive efficiency and innovation.
By meticulously analyzing production data, manufacturers can pinpoint inefficiencies and optimize operations.
- Unveiling Process Insights: Analytics can identify bottlenecks, predict equipment failures, and suggest improvements by aggregating and analyzing data from various stages of the manufacturing process. This capability is crucial for preemptive maintenance and minimizing downtime.
- Case Studies:
- Automotive Assembly Efficiency: A major automotive manufacturer used data analytics to reduce assembly line bottlenecks. By analyzing time-stamped data from the assembly process, the company identified delays in parts supply and optimized the workflow, resulting in a 15% increase in production speed.
- Textile Manufacturer Waste Reduction: A textile company implemented real-time data analytics to monitor raw material usage and product quality. The insights obtained allowed them to adjust their processes, significantly reducing waste and improving product consistency.
AI-Driven Simulation Models
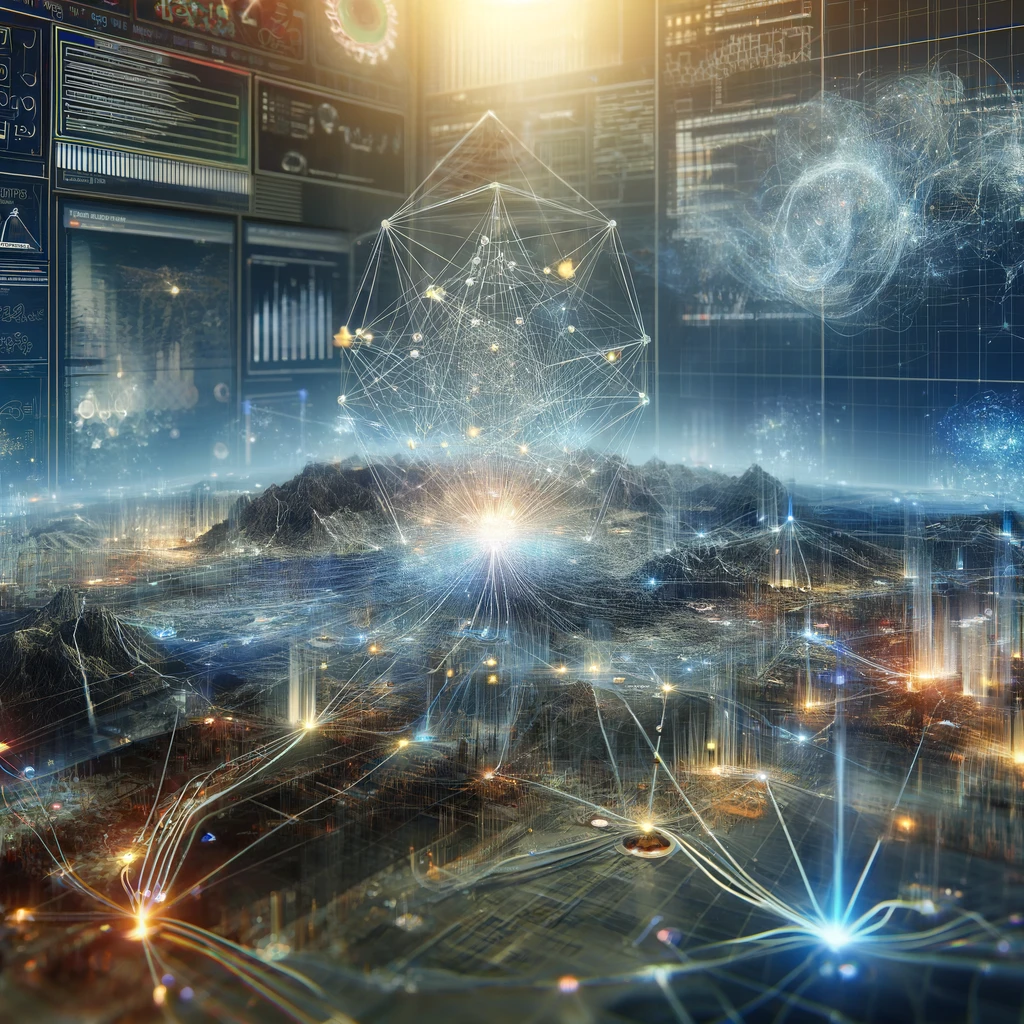
AI-driven simulation models stand at the forefront of manufacturing innovation, offering a powerful tool for optimizing production lines.
These models use artificial intelligence to simulate various production scenarios, enabling manufacturers to foresee outcomes and make informed decisions without costly physical trials.
- Predicting and Testing Scenarios: Simulation models can replicate the manufacturing environment and test configurations, schedules, and operational changes. This predictive capability is invaluable for planning and decision-making.
- Examples of Breakthroughs:
- Pharmaceutical Production Optimization: A pharmaceutical company utilized AI-driven simulation to redesign its drug production process. The model tested different equipment configurations and operational schedules, ultimately identifying a setup that increased output by 20% while maintaining compliance with stringent quality standards.
- Electronics Manufacturer Efficiency: An electronics manufacturer applied simulation models to optimize their assembly line for a new product launch. The simulations identified the most efficient assembly sequence and equipment arrangement, reducing the production cycle by 25% and significantly lowering the initial production costs.
By leveraging data analytics and AI-driven simulation models, manufacturers can gain unprecedented visibility into their operations and explore optimization scenarios in a risk-free environment.
These technologies enhance production efficiency, reduce waste, and propel the manufacturing sector towards a more innovative and sustainable future.
Impact on Production Efficiency and Waste Reduction
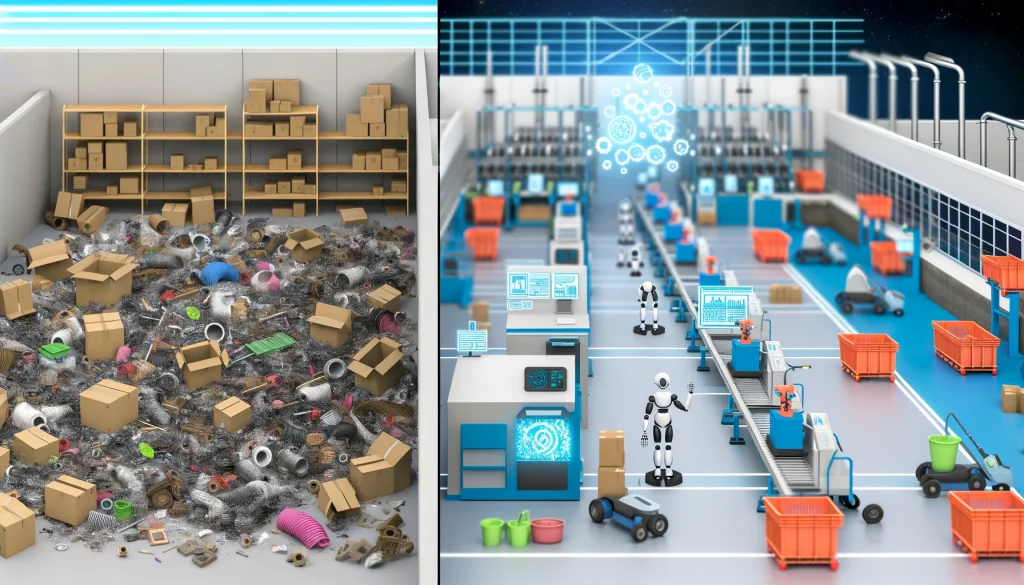
Adopting AI-driven optimization in manufacturing has ushered in significant enhancements in production efficiency and waste reduction.
This is marking a pivotal shift in how manufacturers approach production and sustainability.
- Increased Production Efficiency: AI applications streamline operations, from predictive maintenance reducing downtime to algorithms optimizing production flows, thereby increasing output rates. Manufacturers can now meet higher demand with the same resources, effectively boosting their operational capacity.
- Reductions in Waste: AI’s precision in forecasting demand and optimizing material use leads to less overproduction and material waste. This waste reduction can lead to substantial cost savings in processes where raw material costs are a significant portion of total expenses.
- Contribution to Bottom Line: Enhanced efficiency and reduced waste directly affect the company’s profitability. Lower operational costs and improved output translate to a healthier bottom line, making businesses more competitive and resilient.
- Environmental Sustainability: AI-driven processes contribute to a manufacturer’s environmental sustainability efforts by minimizing waste and optimizing energy use. This helps reduce the environmental footprint and aligns with consumer and regulatory demands for greener manufacturing practices.
Implementing AI in Production Line Optimization
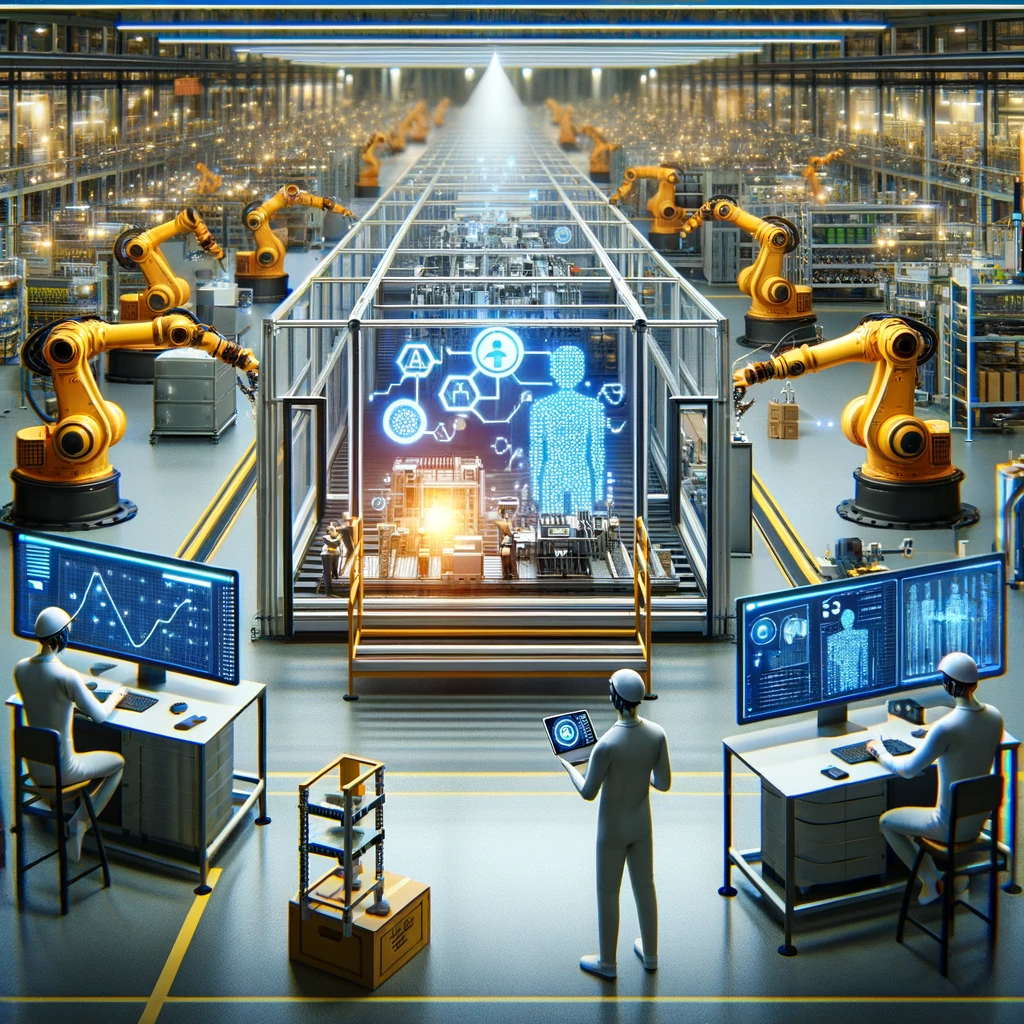
Integrating AI into manufacturing processes is a strategic move that requires careful planning and execution.
Here are the steps and considerations for a successful implementation:
Steps for Integration:
- Assessment and Goal Setting: Begin by thoroughly assessing current production processes to identify inefficiencies. Set clear goals for what AI should achieve: reducing downtime, increasing output, or minimizing waste.
- Selecting AI Solutions: Choose AI tools and technologies that best match your needs. This may involve predictive analytics for maintenance, machine learning for process optimization, or simulation models for planning.
- Data Preparation: Ensure the data needed to train and run AI models is available, accurate, and clean. AI’s effectiveness is directly tied to the quality of data it uses.
- System Integration: Work with IT specialists to integrate AI solutions with existing production and IT infrastructure. Seamless integration ensures that AI tools can effectively communicate with production systems.
- Pilot Testing: Before a full rollout, pilot tests of the AI implementation in selected production areas should be conducted. This allows for identifying and resolving any issues in a controlled environment.
- Training and Change Management: Train employees on how to work with new AI-enhanced processes and manage the change to ensure buy-in from all levels of the organization. Adequate training ensures staff can effectively interact with AI systems and interpret their outputs.
Considerations:
- Data Quality and Availability: The success of AI implementations heavily depends on the availability of high-quality data. Investments may be required to upgrade data collection and management systems.
- System Compatibility: Ensure the AI solutions are compatible with existing manufacturing and IT systems to avoid costly overhauls.
- Ongoing Support and Maintenance: Plan for the ongoing support and maintenance of AI systems, including regular updates and training for users to adapt to system improvements.
By thoughtfully implementing AI technologies, manufacturers can realize significant gains in efficiency and sustainability. Positioning themselves for success in an increasingly competitive and environmentally conscious market.
Challenges and Future Directions
Adopting AI for production line optimization comes with its set of challenges, but it also opens the door to exciting future possibilities:
- Technological Complexity: Implementing AI solutions requires a deep understanding of technology and manufacturing processes. For some manufacturers, integrating AI with existing systems can be daunting.
- Solution: Investing in training and partnering with experienced AI providers can help overcome this hurdle.
- Investment Costs: The initial investment in AI technology, including hardware, software, and expertise, can be significant.
- Mitigation: Calculating the ROI and exploring financing options can help justify the investment through long-term savings and efficiency gains.
Future Predictions:
- Emerging Technologies: The Internet of Things (IoT), advanced robotics, and edge computing will likely converge with AI to create even more sophisticated manufacturing ecosystems.
- New Applications: AI’s role will expand beyond optimization to encompass entire manufacturing lifecycles, from design to after-sales service, enabling fully automated and highly personalized production processes.
FAQs
How can I identify bottlenecks in my production line?
Look closely at your production processes to find steps where delays frequently occur. Use data analysis and observations to pinpoint these areas.
What benefits does automation bring to the production line?
Automation introduces machinery for repetitive tasks, which increases both the speed and the consistency of those tasks.
How can I organize my production process to reduce delays?
Rearrange your production process to ensure smooth transitions between each step, minimizing waiting times and material handling.
Why is employee training important for optimizing production lines?
Training equips your workforce with the necessary skills and knowledge to perform tasks more effectively and safely, improving output quality and speed.
How often should I review and adjust my production processes?
Regular assessments are crucial. Analyze performance data frequently to identify areas for improvement and make necessary adjustments.
What role does quality control play in production line optimization?
Implementing stringent quality control measures at various stages helps reduce errors and rework, maintaining a steady production flow.
Can optimizing layout improve production line performance?
Redesigning the layout to reduce movement and facilitate easier access to materials can significantly reduce wasted time and effort.
How does predictive maintenance contribute to production optimization?
Predictive maintenance prevents downtime by anticipating machinery failures before they happen, keeping the production line running smoothly.
What impact does inventory management have on production efficiency?
Effective inventory management ensures that materials are available when needed, preventing production halts due to shortages or excess inventory.
How can I make my production line more adaptable to changes?
Incorporating modular designs and flexible processes allows quicker adjustments to production lines in response to changing demands or products.
What is the significance of cross-training employees?
Cross-training employees enables them to perform multiple roles, increasing the flexibility and adaptability of your workforce.
How can technology improve communication on the production floor?
Utilizing modern communication tools and systems enhances coordination and information sharing among team members, leading to smoother operations.
What strategies can reduce material waste in production?
Implementing lean manufacturing principles and closely monitoring material use can significantly reduce waste and improve cost-effectiveness.
How does customer feedback influence production line optimization?
Customer feedback can provide valuable insights into quality and design improvements, guiding adjustments to effectively meet market demands.
What is the role of leadership in successful production line optimization?
Strong leadership is essential for setting clear goals, motivating the team, and fostering a culture of continuous improvement and innovation.